Dead-time distortion
Dead time distortion (DTD) is some times a significant problem in all PWM based drives.
Contents
[hide]Phenomenon
Dead time distortion is present in some extent in all half-bridge topology PWM power outputs.
Description of the image:
- Schematic: typical single phase half-bridge PWM power output consisting two transistors and an inductive load (inductor). In 3 phase motor drives there are 3 pcs of this kind of circuits excluding inductor (which is replaced by a motor coil).
- Desired load voltage waveform: the distortion free waveform reference signal on load that we would want to see.
- PWM to top transistor: PWM signal that is controls when the top side transistor is in conductive state.
- PWM to bottom transistor: PWM signal that is controls when the bottom side transistor is in conductive state.
- Grey areas: time when neither of PWM signals are in "on" state making both transistor non-conductive. This is necessary to prevent on-state overlapping and shoot-through currents from V+ to GND.
- Positive current load voltage: this is the achieved (distorted) PWM signal on load when current direction is positive in load inductor.
- Negative current load voltage: this is the achieved (distorted) PWM signal on load when current direction is negative in load inductor.
As it figure shows, actual output voltage differs from desired load voltage. Actual PWM duty cycle either becomes higher or lower than desired and distortion direction changes whenever current direction reverses.
Distortion effects
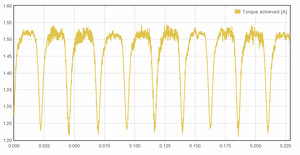
Some of most notable problems caused by DTD:
- Causes ripple in torque response and can be seen in measurements and motor performance.
- Causes "electrical backlash" or laziness for motor control. With DTD, motor reaction time is significantly increased whenever current direction is reversed (such as motor is reversing direction). This increases tracking error of servo motor.
- More difficulty in proper servo tuning.
- Reduced servo stiffness.
Measurements
Dead time distortion without countermeasures
These graphs show actual distortion on sinusoidal motor currents when PWM frequency was 17.5 kHz and dead-time length 2 µs. No countermeasures were taken to reduce distortion.
Notice how PWM duty cycle reference jumps up/down trying to compensate dead time errors. However, no current controller alone is fast enough to completely eliminate current ripples.
Dead time distortion with countermeasures
This is the exactly same experiment with the one above but this time VSD-XR dead time correction was turned on. Notice how dips almost completely disappear and PWM duty cycle reference shows more sine-like waveform.
In no event the Product Information or parts hereof shall be regarded as guarantee of conditions or characteristics. The Product Information or any part thereof may also not be regarded as a warranty of any kind. No liability of any kind shall be assumed by Author with respect to Product Information or any use made by you thereof, nor shall Author indemnify you against or be liable for any third party claims with respect to such information or any use thereof.
As content of this Wiki may be edited by user community, Granite Devices Oy or it's affiliates do not take any responsibility of the contents of this Wiki. Use information at your own risk. However, Granite Devices staff attempts to review all changes made to this Wiki and keep information trustworthy.
Without written consent, Granite Devices' Products or Intellectual Property shall not be used in situations or installations where living beings, material property, or immaterial property could be harmed by the operation, features or failures of Product. Products may only be used in a way where hazards like moving parts, electric shock, laser radiation, or fire can't be realized even if the content of this Wiki would suggest otherwise.