Difference between revisions of "IONICUBE connectors and pinouts"
From Granite Devices Knowledge Wiki
[checked revision] | [checked revision] |
(→Front connectors) |
(→Back connectors) |
||
Line 96: | Line 96: | ||
==Back connectors== | ==Back connectors== | ||
+ | Back side connectors consists: | ||
+ | ;X1 | ||
+ | :Dual port RJ45 connector with [[SimpleMotion V2]] interface. For pinout, see[[SimpleMotion V2 port]]. | ||
+ | ;X2 | ||
+ | :6 pin wire terminal for logic voltage supply, [[Safe torque off]] input, analog output and relay driver outputs. | ||
+ | ;X3 | ||
+ | :Two pin wire terminal for [[HV DC bus]] supply. | ||
+ | ;X4 | ||
+ | :Main control and [[setpoint]] signal port consisting Enable input signal, Fault output signal, [[pulse & direction]]/[[quadrature]]/[[PWM]] setpoint inputs and digital outputs for home switch status. X4 is directly wired to conform most common parallel port style pulse & direction CNC controllers. | ||
+ | ;X5 | ||
+ | :Second control and [[setpoint]] signal port. This port consists analog setpoint signal inputs and additional digital I/O. | ||
+ | |||
{{picturebox|Ionicube x2345.png|caption=A closeup of X2, X3, X4 and X5}} | {{picturebox|Ionicube x2345.png|caption=A closeup of X2, X3, X4 and X5}} | ||
− | ===X2=== | + | {{damage|Never connect an Ethernet to X1. While it uses similar connector and cabling, it is electrically incompatible with Ethernet. Devices may be permanently damaged by mixing Ethernet and SimpleMotion V2.}} |
+ | {{damage|Do now wire SimpleMotion V2 ports with [http://en.wikipedia.org/wiki/Ethernet_crossover_cable crossover RJ45 cables (see details)]. Always use straight/non-crossover patch cables. If unsure about what is the type of your RJ45 cable, don't use it.}} | ||
+ | |||
+ | ===X2 pinout=== | ||
{| class="wikitable" | {| class="wikitable" | ||
|- | |- | ||
Line 115: | Line 130: | ||
| 6|| class="outpin"|RL2 || Relay coil driver output 2. When RLIN2 on X4 is logic high, RL2 is pulled to GND by an open collector circuit. When RLIN1 is low, RL2 is floating (max 24V). | | 6|| class="outpin"|RL2 || Relay coil driver output 2. When RLIN2 on X4 is logic high, RL2 is pulled to GND by an open collector circuit. When RLIN1 is low, RL2 is floating (max 24V). | ||
|} | |} | ||
− | ===X3=== | + | ===X3 pinout=== |
{| class="wikitable" | {| class="wikitable" | ||
|- | |- | ||
Line 125: | Line 140: | ||
|} | |} | ||
− | ===X4=== | + | ===X4 pinout=== |
{| class="wikitable" | {| class="wikitable" | ||
! Pin number in header!!Pin number in D25 cable!!Signal name!!Typical usage | ! Pin number in header!!Pin number in D25 cable!!Signal name!!Typical usage | ||
Line 158: | Line 173: | ||
|} | |} | ||
− | ===X5=== | + | ===X5 pinout=== |
{| class="wikitable" | {| class="wikitable" | ||
! Pin number in header!!Pin number in D25 cable!!Signal name!!Typical usage | ! Pin number in header!!Pin number in D25 cable!!Signal name!!Typical usage |
Revision as of 22:00, 26 March 2015
Contents
[hide]Front connectors
Front side connectors consist X6, X7, X8 and X9. These connectors are the interface towards motors (motor power and feedback devices).
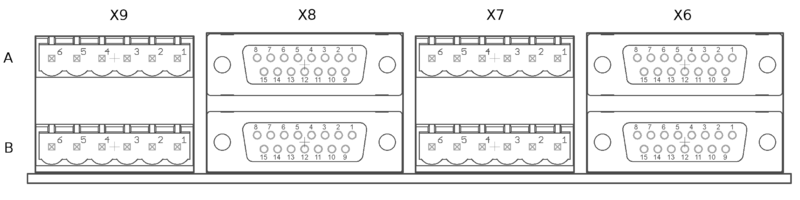
Names of power and feedback ports. I.e. X9A means upper floor connector of X9 and X9B the lower floor of X9.
Legend
Color |
---|
Supply pin |
Input pin |
Output pin |
X7 and X9 pinout
Pin number | Signal name | Usage |
---|---|---|
1 | GND | Ground for cable shield and an optional motor holding brake coil |
2 | PHASE1 | Motor phase 1 |
3 | PHASE2 | Motor phase 2 |
4 | PHASE3 | Motor phase 3 |
5 | PHASE4 | Motor phase 4 |
6 | BRAKE | 24V motor holding brake coil drive |
Motor & brake wiring schematics
X6 and X8 pinout
Pin # | Pin name | Electrical type (in most feedback device modes) | Alternate electrical type (in some feedback device modes) | Connection with various feedback devices |
---|---|---|---|---|
Shell | GND | Earth/case | Feedback cable shield | |
1 | HALL_W | Digital input W | Hall sensor input, phase W | |
2 | HALL_V | Digital input V | Hall sensor input, phase V | |
3 | HALL_U | Digital input U | Hall sensor input, phase U | |
4 | GND | Encoder supply ground | ||
5 | B- | Differential input B- | Analog input B+ | Quadrature encoder (B channel)/SinCos/serial encoder/resolver input |
6 | B+ | Differential input B+ | Analog input B- | |
7 | A- | Differential input A- | Analog input A- | Quadrature encoder (A channel)/SinCos/serial encoder/resolver input |
8 | A+ | Differential input A+ | Analog input A+ | |
9 | 5V_OUT | Encoder supply 5V output | Encoder power supply | |
10 | GND | Encoder supply ground | ||
11 | GPI3 | Axis negative direction end limit switch (optional) | Connect normally closed (NC) limit switch between this pin and GND pin | |
12 | GPI2 | Axis positive direction end limit switch (optional) | Connect normally closed (NC) limit switch between this pin and GND pin | |
13 | GPI1 | Axis home switch switch (optional) | Connect normally closed (NC) limit switch between this pin and GND pin | |
14 | C- | Differential input C- | Quadrature encoder index channel (Z channel)/serial encoder input | |
15 | C+ | Differential input C+ |
Examples of feedback device and switch wiring
![]() | In case of single-ended encoder, connect encoder's A, B, Z only to drive's A+, B+ and C+ and leave drive's A-, B- and C- unconnected. |
![]() | With differential Hall sensor (which provides U+, U-, V+, V-, W+ and W-, connect only sensor's U+, V+ and W+ to drive's HALL_U/V/W. |
![]() | Never connect sensor negative outputs (A-/B-/C-/U-/V-/W-) to GND. Connect them to drive's A-/B-/C- or leave unconnected. |
![]() | Feedback devices with differential signaling may use varying naming schemes of signal pairs. For example differential signal X (which contains two electrical wires) may be denoted as: X+ and X-, or X and \X or X and X. In this Wiki we mark them X+ and X-. Some Fanuc encoders have quadrature signals named as PCA, /PCA, PCB, /PCB, PCZ and /PCZ which are equivalent to A, B and Z signal pairs. |
Back connectors
Back side connectors consists:
- X1
- Dual port RJ45 connector with SimpleMotion V2 interface. For pinout, seeSimpleMotion V2 port.
- X2
- 6 pin wire terminal for logic voltage supply, Safe torque off input, analog output and relay driver outputs.
- X3
- Two pin wire terminal for HV DC bus supply.
- X4
- Main control and setpoint signal port consisting Enable input signal, Fault output signal, pulse & direction/quadrature/PWM setpoint inputs and digital outputs for home switch status. X4 is directly wired to conform most common parallel port style pulse & direction CNC controllers.
- X5
- Second control and setpoint signal port. This port consists analog setpoint signal inputs and additional digital I/O.
![]() | Never connect an Ethernet to X1. While it uses similar connector and cabling, it is electrically incompatible with Ethernet. Devices may be permanently damaged by mixing Ethernet and SimpleMotion V2. |
![]() | Do now wire SimpleMotion V2 ports with crossover RJ45 cables (see details). Always use straight/non-crossover patch cables. If unsure about what is the type of your RJ45 cable, don't use it. |
X2 pinout
Pin number | Signal name | Usage |
---|---|---|
1 | GND | Ground |
2 | 24V | 24V logic supply |
3 | STO | Safe torque off input (this pin also available in X1, as defined in SimpleMotion V2 port |
4 | VFD | 0-12V analog output where voltage level is proportional to PWM duty cycle on pin PWM on X4. PWM frequency must be between 100 and 10000 Hz. |
5 | RL1 | Relay coil driver output 1. When RLIN1 on X4 is logic high, RL1 is pulled to GND by an open collector circuit. When RLIN1 is low, RL1 is floating (max 24V). |
6 | RL2 | Relay coil driver output 2. When RLIN2 on X4 is logic high, RL2 is pulled to GND by an open collector circuit. When RLIN1 is low, RL2 is floating (max 24V). |
X3 pinout
Pin number | Signal name | Usage |
---|---|---|
1 | GND | Ground |
2 | HV+ | Motor power supply, HV DC bus (see IONI drive voltage range spec) |
X4 pinout
Pin number in header | Pin number in D25 cable | Signal name | Typical usage | Pin number in header | Pin number in D25 cable | Signal name | Typical usage | |
---|---|---|---|---|---|---|---|---|
1 | 1 | ENABLE | Enable all axis (with or without chargepump) | 2 | 14 | PWM | PWM input for VFD analog output | |
3 | 2 | HSIN1_X | Direction input X | 4 | 15 | GPO4_A | Limit switch output A | |
5 | 3 | HSIN2_X | Pulse/step input X | 6 | 16 | RLIN1 | Controls RL1 state | |
7 | 4 | HSIN1_Y | Direction input Y | 8 | 17 | RLIN2 | Controls RL2 state | |
9 | 5 | HSIN2_Y | Pulse/step input Y | 10 | 18 | GND | Ground | |
11 | 6 | HSIN1_Z | Direction input Z | 12 | 19 | GND | ||
13 | 7 | HSIN2_Z | Pulse/step input A | 14 | 20 | GND | ||
15 | 8 | HSIN1_A | Direction input A | 16 | 21 | GND | ||
17 | 9 | HSIN2_A | Pulse/step input A | 18 | 22 | GND | ||
19 | 10 | STOP_OUT | Fault on any axis or E-stop (active low) | 20 | 23 | GND | ||
21 | 11 | GPO4_X | Limit switch output X | 22 | 24 | GND | ||
23 | 12 | GPO4_Y | Limit switch output Y | 24 | 25 | GND | ||
25 | 13 | GPO4_Z | Limit switch output Z | 26 | N/A | Not connected |
X5 pinout
Pin number in header | Pin number in D25 cable | Signal name | Typical usage | Pin number in header | Pin number in D25 cable | Signal name | Typical usage | |
---|---|---|---|---|---|---|---|---|
1 | 1 | GND | 2 | 14 | +5V_OUT | 5V supply from IONICUBE ^2 | ||
3 | 2 | ANAIN-_X | +/-10V analog input X | 4 | 15 | ANAIN+_X | +/-10V analog input X | |
5 | 3 | ANAIN-_Y | +/-10V analog input Y | 6 | 16 | ANAIN+_Y | +/-10V analog input Y | |
7 | 4 | ANAIN-_Z | +/-10V analog input Z | 8 | 17 | ANAIN+_Z | +/-10V analog input Z | |
9 | 5 | ANAIN-_A | +/-10V analog input A | 10 | 18 | ANAIN+_A | +/-10V analog input A | |
11 | 6 | GPO1_X | For pin function, refer to IONI connector pinout | 12 | 19 | GPI4_X | For pin function, refer to IONI connector pinout | |
13 | 7 | GPO1_Y | 14 | 20 | GPI4_Y | |||
15 | 8 | GPO1_Z | 16 | 21 | GPI4_Z | |||
17 | 9 | GPO1_A | 18 | 22 | GPI4_A | |||
19 | 10 | GPO5_X | 20 | 23 | GPI5_X | |||
21 | 11 | GPO5_Y | 22 | 24 | GPI5_Y | |||
23 | 12 | GPO5_Z | 24 | 25 | GPI5_Z | |||
25 | 13 | GPO5_A | 26 | N/A | GPI5_A |
A typical connection with legacy parallel port style CNC controller such as Mach3/Mach4/LinuxCNC. A 26 pin ribbon cable may be directly connected to PC parallel port or to equivalent pinout step/dir generator such as SmoothStepper.