Troubleshooting position control faults
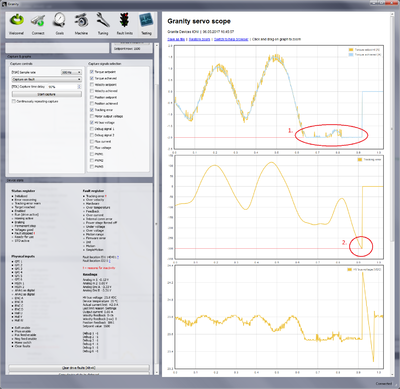
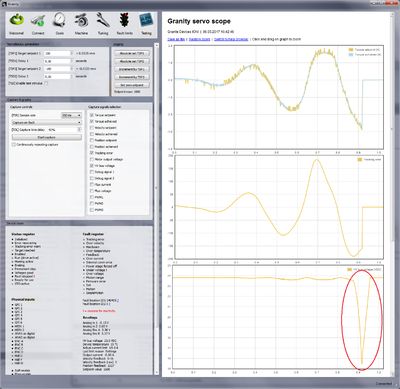
Position control fault can occur due to several reasons. This page gives tips how to troubleshoot the reason of the fault.
Using fault status information
Method for finding the root cause of the fault: check Fault location from Granity Testing tab (scroll down the page to find Fault location numbers). This indicates the fault that occurred first of all faults, and is likely the reason causing rest of the faults as well.
Some most typical reasons that may happen:
- Insufficient torque on motor: motor will lag behind if it is not allowed to produce enough torque to overcome load resistance (see scope examples below). Solutions: decrease acceleration/velocity rates or increase motor current limits to get more torque.
- Undervoltage fault: HV DC bus power supply dropped voltage under the load and caused drive to fault stop
- Tracking error occurred: too tight tracking error tolerance (see Position tracking error thresholdFPT) and Servo motor tuning guide
Using Granity scope
One of most effective ways to find reason for fault is to use scope capture in Granity. In this example, we capture signals revealing fault reason in example cases:
- Choose Capture on fault as trigger
- Choose quite low sample rate, such as 500 Hz
- Choose channels Torque achieved, Torque setpoint, HV bus voltage and Tracking error
- Untick Continuously repeating capture
- Start capture
- Perform the operation that causes the fault
If you can't reproduce the fault while Granity is connected, you may use the offline capture feature.
![]() | The method above is most effective with latest firmware version and Granity version that support offline capture and capture trigger delay. In older versions Capture on fault records data only after the fault, which may not provide very useful information, while the new version records also events before the fault.
|
In no event the Product Information or parts hereof shall be regarded as guarantee of conditions or characteristics. The Product Information or any part thereof may also not be regarded as a warranty of any kind. No liability of any kind shall be assumed by Author with respect to Product Information or any use made by you thereof, nor shall Author indemnify you against or be liable for any third party claims with respect to such information or any use thereof.
As content of this Wiki may be edited by user community, Granite Devices Oy or it's affiliates do not take any responsibility of the contents of this Wiki. Use information at your own risk. However, Granite Devices staff attempts to review all changes made to this Wiki and keep information trustworthy.
Without written consent, Granite Devices' Products or Intellectual Property shall not be used in situations or installations where living beings, material property, or immaterial property could be harmed by the operation, features or failures of Product. Products may only be used in a way where hazards like moving parts, electric shock, laser radiation, or fire can't be realized even if the content of this Wiki would suggest otherwise.