Argon Servo Drive
Versatile servo drive ARGON supports virtually any type of industrial servo motor including AC, Brushless DC, Brush DC and Linear motors.
Whether the application requires position, velocity or torque operating mode, Argon handles them all out-of-the-box. Built-in motion profiler enables simple point-to-point moves as well as continuous synchronous motion tracking.
This product is at its End of Life.
Motor's best friend
See how Argon changes the way servo motors are controlled in 2016
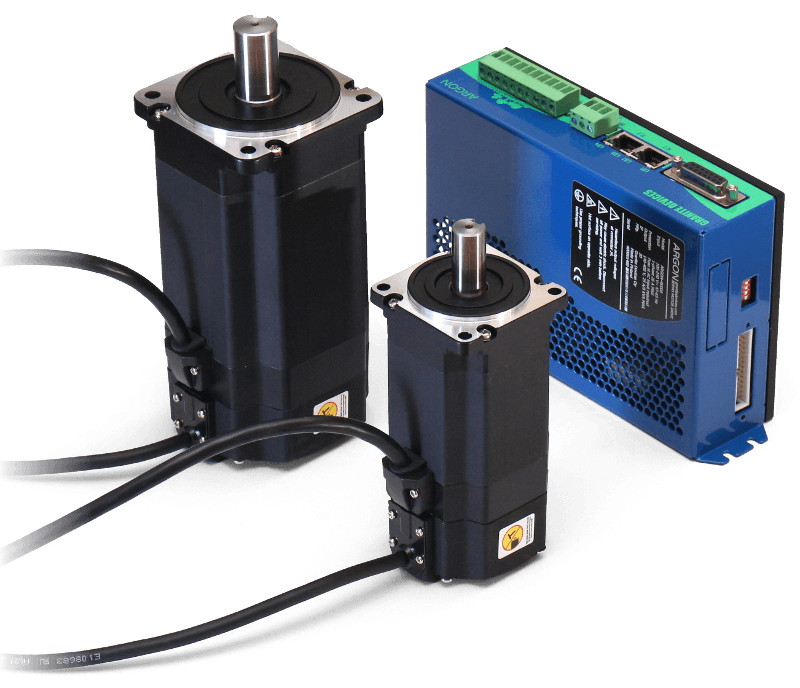
- High dynamic range torque control
Maximized versatility - thanks to HDRT, a single model drives AC, BLDC, Linear and DC servo motors from 50 W to 1500 W
- Open source architecture
Argon has an dedicated ARM CPU for user's custom functionality
- Eliminate axis limit switches
Internal axis homing function with sensorless hard-stop detection mode and soft travel limits eliminates the need of physical end-of-travel switches and their wiring
- Ruggedness taken to the max
Device protections include over current, short circuit, over voltage, under voltage, over temperature and I2t protections, internal fuse and communication error detection
- Safety built in
3-way redundant safe torque off with motor braking
The value of simplicity
ARGON reduces the number of motion control components to the bare minimum. A typical PC controlled multiaxis system can be implemented by using direct USB or RS485 driven SimpleMotion field bus to the servo drives. The same bus carries a dedicated safety stopping circuit without additional wiring. The wiring scheme is compatible with IONI drive allowing mixing different kinds of drives.
In addition to SimpleMotion bus, ARGON also reads traditional control signals, such as pulse & direction, PWM, and analog velocity reference out of the box. In such case, SimpleMotion is only used for drive configuration with Granity.
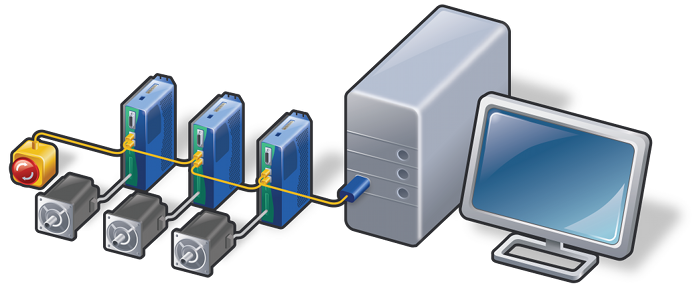
Everything included
Hardware of Argon has been designed from ground up without any historical payload. This not only costs less but also yields unforeseen flexibility and reliability.

Real-time requirements? Not one of your problems.
Implement your multi-axis motion control application with SimpleMotion buffered motion stream API and break free from the need of real-time motion controller.
User application just fills-up drive buffers with position setpoints and drives will run the commands synchronously based on their internal precision clocks. This allows host motion controller to be just an ordinary non-realtime PC application.
Best of all? Everything can be done over omnipresent USB or RS485 port.
If hard real-time control is required, SimpleMotion bus also supports instantenous commands up to 20 kHz command rate.
Configuration tool that makes you smile
Goodbye frustration, hello future! Granity makes setup and tuning of servo motor a breeze. Combined with walk-through online documentation, motors are fully configured and running in the industry record time.
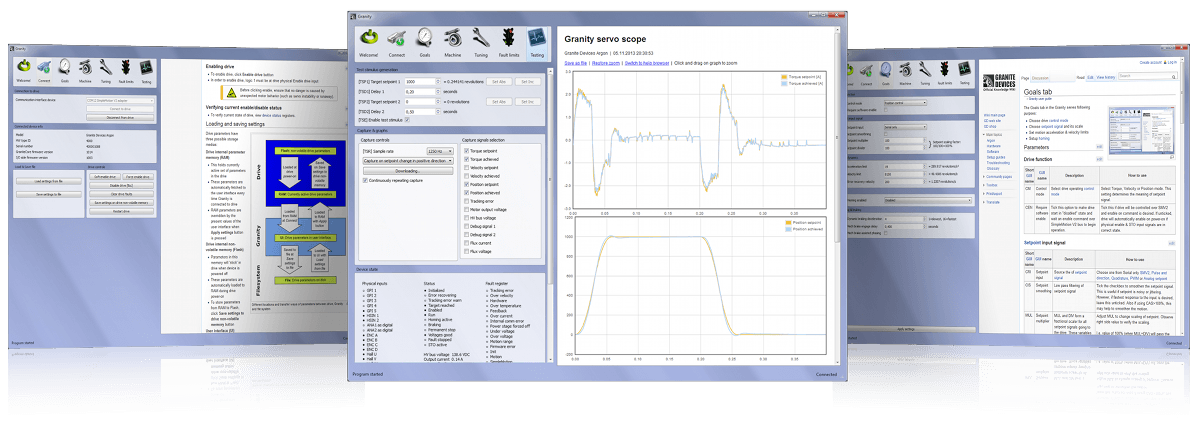
How it compares
Drive | IONI | IONI Pro | IONI Pro HC | ARGON |
Mates with | Low voltage servo or stepping motors. See motor compatibility guide. | Low voltage servo or stepping motors. See motor compatibility guide. | Low voltage servo or stepping motor. See motor compatibility guide. | High voltage servo motors. See motor compatibility guide. |
Motors | AC, BLDC, DC, Linear, Stepper | AC, BLDC, DC, Linear, Stepper | AC, BLDC, DC, Linear, Stepper | AC, BLDC, DC, Linear |
Output power |
250 W passive cooling 500 W forced air cooling |
250 W passive cooling 600 W forced air cooling |
350 W passive cooling 800 W forced air cooling |
600 W passive cooling 1800 W forced air cooling |
Motor size |
5 – 400 W | 5 – 500 W | 20 – 700 W | 50 – 1500 W |
Control modes | Torque, Velocity, Position | Torque, Velocity, Position | Torque, Velocity, Position | Torque, Velocity, Position |
Safe torque off |
2-way, SIL2+ compliant | 2-way, SIL2+ compliant | 2-way, SIL2+ compliant | 3-way, SIL2+ compliant |
Control sources | SimpleMotion V2, pulse & direction, quadrature, analog, PWM | SimpleMotion V2, EtherCAT*, pulse & direction, quadrature, analog, PWM | SimpleMotion V2, EtherCAT*, pulse & direction, quadrature, analog, PWM | SimpleMotion V2, EtherCAT*, pulse & direction, quadrature, analog, PWM |
Homing function | Yes, advanced | Yes, advanced | Yes, advanced | Yes, advanced |
Feedback devices | Incremental encoder | Incremental encoders, SinCos encoder (16, 64 and 256X interpolation), Absolute serial encoders: BiSS B, BiSS C, SSI, AMS 5311 | Incremental encoders, SinCos encoder (16, 64 and 256X interpolation), Absolute serial encoders: BiSS B, BiSS C, SSI, AMS 5311 | Incremental encoder, Resolver |
Supply voltage | 5 – 52 VDC | 5 – 52 VDC | 5 – 55 VDC | 85- 264 VAC / 45 – 380 VDC |
Output current | Up to 15 A continuous | Up to 18 A continuous | Up to 25 A continuous | Up to 12 A Continuous, 18 A peak |
Dimensions | 69.5 × 36.5 × 6.5 mm | 69.5 × 36.5 × 6.5 mm | 69.5 × 36.5 × 6.5 mm | 51 × 197 × 127 mm |
Warranty | 12 months | 24 months | 24 months | 24 months |
Buy now | Buy now | Buy now | Buy now |
* feature under development
Kickstart your project
Find all the resources you need from the Granite Devices Wiki
Request a quote
Related products
SimpleMotion API
Maximally simplified but still capable open source motion control library to control all Granite Devices drives on PC or embedded systems. SimpleMotion allows taking full control of all drive features with small amount of code.